Приборы неразрушающего контроля
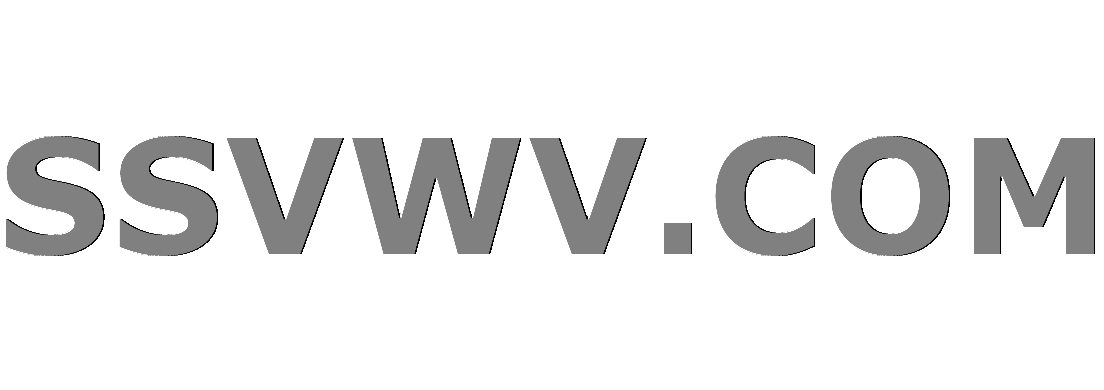
Multi tool use
![]() |
Эту страницу предлагается объединить со страницей Дефектоскоп. |
Прибо́ры неразруша́ющего контро́ля — средства используемые при различных методах неразрушающего контроля для определения свойств и параметров, и оценки надёжности объекта, конструкции или сварного шва.
Содержание
1 Дефектоскопы
2 Импульсные ультразвуковые дефектоскопы
3 Импедансные дефектоскопы
4 Резонансные дефектоскопы
5 Магнитно-порошковые дефектоскопы
6 Вихретоковые дефектоскопы
7 Феррозондовые дефектоскопы
8 Электроискровые дефектоскопы
9 Термоэлектрические дефектоскопы
10 Радиационные дефектоскопы
11 Инфракрасные дефектоскопы
12 Радиоволновые дефектоскопы
13 Электронно-оптические дефектоскопы
14 Капиллярные дефектоскопы
15 Толщиномер
16 Течеискатель
17 Гелиевые масспектрометрические течеискатели
18 Фреоновые течеискатели
19 Литература
20 Примечания
Дефектоскопы |

Прибор для ультразвукового контроля двигателя V2500
Дефектоскоп — прибор неразрушающего контроля для выявления и оценки внутренних и поверхностных дефектов материалов и изделий. В зависимости от метода неразрушающего контроля, дефектоскопы можно классифицировать на вихретоковые, магнитные, ультразвуковые.
Дефектоскоп — устройство для обнаружения дефектов в изделиях из различных металлических и неметаллических материалов методами неразрушающего контроля. К дефектам относятся нарушения сплошности или однородности структуры, зоны коррозионного поражения, отклонения химического состава и размеров и др. Область техники и технологии, занимается разработкой и использованием дефектоскопов называется дефектоскопией. С дефектоскопами функционально связаны и другие виды средств неразрушающего контроля: течеискатели, толщиномеры, твердомеры, Структуроскопы, интроскопы и Стилоскоп.
Импульсные ультразвуковые дефектоскопы |

Испытания сварного шва трубопровода на наличие дефектов с использованием ультразвукового инструмента с фазированной решеткой.
В импульсных дефектоскопах используются эхо-метод, теневой и зеркально-теневой методы контроля. Эхо-метод основан на посылке в изделие коротких импульсов ультразвуковых колебаний и регистрации интенсивности и времени прихода эхо, отраженных от несплошностей (дефектов). Для контроля изделия датчик еходефектоскопа сканирует его поверхность. Метод позволяет обнаруживать поверхностные и глубинные дефекты с различной ориентацией. При теневом методе ультразвуковые колебания, встретив на своем пути дефект, отражаются в обратном направлении. О наличии дефекта судят по уменьшению энергии ультразвуковых колебаний или по изменению фазы ультразвуковых колебаний, огибающих дефект. Метод широко применяют для контроля сварных швов, рельсов и др.
Зеркально-теневой метод используют вместо или в дополнение к эхо-метода для выявления дефектов, дающих слабое отражение ультразвуковых волн в направлении раздельно-совмещенного преобразователя. Дефекты (например, вертикальные трещины), ориентированные перпендикулярно к поверхности, по которой перемещают преобразователь (поверхности ввода), дают очень слабый рассеянный и донный сигналы благодаря тому, что на их поверхности продольная волна трансформируется в главную, которая в свою очередь излучает боковые волны, уносящие энергию. Пример применения зеркально-теневого метода — контроль рельсов на вертикальные трещины в шейке. По чувствительности этот метод обычно в 10-100 раз хуже эхо-метода.
При контроле сварных соединений необходимо обеспечивать тщательное прозвучивание всего шва металла. Ультразвуковые волны вводятся в шов через основной металл с помощью наклонных акустических преобразователей. При поиске дефектов делают продольно-поперечное перемещение (сканирование) преобразователя вдоль шва, одновременно осуществляя его вращательное движение. Чувствительность ультразвукового контроля определяется минимальными размерами выявленных дефектов или эталонных отражателей (моделей дефектов). В качестве эталонных отражателей обычно используют плоскодонные сверления, ориентированные перпендикулярно направлению прозвучивания, а также боковые сверления или зарубки.
Импедансные дефектоскопы |
Принцип работы основан на определении различия полного механического сопротивления (импеданса) дефектного участка по сравнению с доброкачественным, для чего контролируемая поверхность сканируется с помощью двух пьезоэлементов, один из которых возбуждает колебания в материале, а другой воспринимает колебания. Импедансные дефектоскопы предназначены для выявления дефектов, расслоений, пористости и нарушения целостности композитных материалов и сотовых структур в авиастроении, космической, автомобильной и других отраслях промышленности.
Резонансные дефектоскопы |
Резонансный метод основан на определении собственных резонансных частот упругих колебаний (частотой 1 — 10 МГц) при возбуждении их в изделии. Этим методом измеряют толщину стенок металлических и некоторых неметаллических изделий. При возможности измерения с одной стороны погрешность измерения — около 1 %. Кроме того, с помощью резонансной дефектоскопии можно выявлять зоны коррозионного поражения. Вариантом резонансного метода является спектрально-акустическая дефектоскопия .
Магнитно-порошковые дефектоскопы |

Распределение магнитного поля вокруг дефекта в ферромагнитном материале
Дефектоскоп позволяет контролировать различные по форме детали, сварные швы, внутренние поверхности отверстий путем намагничивания отдельных контролируемых участков или изделия в целом циркулярным или продольным полем, создаваемым с помощью набора намагничивается устройств, питающихся импульсным или постоянным током, или с помощью постоянных магнитов. Принцип действия основан на создании поля рассеяния над дефектами контролируемой детали с последующим выявлением их магнитной суспензией. Наибольшая плотность магнитных силовых линий поля рассеяния наблюдается непосредственно над трещиной (или над другой несплошное) и уменьшается с удалением от неё[1].
Для выявления несплошности на поверхность детали наносят магнитный порошок, взвешенный в воздухе (сухим способом) или в жидкости (мокрым способом). На долю в поле рассеяния будут действовать силы: магнитного поля, направленная в область наибольшей плотности магнитных силовых линий, то есть до места расположения трещины; тяжести; выталкивающей действия жидкости; трения; силы электростатического и магнитного взаимодействия, возникающих между частицами. В магнитном поле частицы намагничиваются и соединяются в цепочки. Под действием результирующей силы частицы притягиваются к трещине и накапливаются над ней, образуя скопления порошка. Ширина полоски (валика) с оседлой порошка значительно больше ширины раскрытия трещины. По этому осаждению (индикаторному рисунку) определяют наличие дефектов.
Вихретоковые дефектоскопы |
Принцип действия основан на методе вихревых токов, который заключается в нарушении вихревых токов в локальной зоне контроля и регистрации изменений электромагнитного поля вихревых токов, обусловленных дефектом и электрофизическими свойствами объекта контроля. Характеризуется небольшой глубиной контроля. Используется для обнаружения трещин и несплошности материала на глубине до 2 мм.
Феррозондовые дефектоскопы |
Феррозондовые используют метод магнитной дефектоскопии, основанный на том, что при движении феррозондовые (чувствительного элемента, реагирующего на изменение магнитного поля) вдоль изделия производятся импульсы тока, форма которых зависит от наличия дефектов в изделии. Высокая чувствительность дефектоскопов-градиентометры позволяет выявлять дефекты с шириной раскрытия в несколько микрометров и глубиной от 0,1 мм. Возможно выявление дефектов немагнитным покрытием толщиной до 6 мм. Шероховатость контролируемых поверхностей — до Rz 320 мкм. Дефектоскопы-градиентометры применяются для контроля литых деталей, проката, сварных соединений.
Электроискровые дефектоскопы |
Принцип действия основан на электрическом пробое воздушных промежутков между соприкасающимися поверхностями изоляционного покрытия щупом, подключенным к одному полюсу источника высокого напряжения, и диагностируются объектом, подключенным к другому полюсу источника высокого напряжения непосредственно или через почву с помощью заземления.
Термоэлектрические дефектоскопы |
Принцип действия термоэлектрических дефектоскопов основан на измерении ЭДС (термо-ЭДС), возникающая в замкнутой цепи при нагреве места контакта двух разнородных материалов. Если один из этих материалов принять за эталон, то при заданной разности температур горячего и холодного контактов величина и знак термо-ЭДС определяться химическим составом второго материала. Этот метод обычно применяют в тех случаях, когда нужно определить марку материала, из которого состоит полуфабрикат или элемент конструкции (в том числе, в готовой конструкции).
Радиационные дефектоскопы |
В радиационных дефектоскопах осуществляется облучения объектов рентгеновскими, α, β и γ лучами, а также нейтронами. Источники излучений — рентгеновские аппараты, радиоактивные изотопы, линейные ускорители, Бетатрон, Микротрон. Радиационное изображение дефекта превратят в радиографический снимок (радиография), электрический сигнал (радиометрия) или световое изображение на выходном экране радиационно-оптического преобразователя или прибора (радиационная интроскопия, радиоскопия).
Первый радиационный дефектоскоп был внедрен в 1933 году на Балтийском судостроительном заводе изобретателем Л. В. Мысовскую и использовался для выявления дефектов литья в толстых металлических плитах к печам «Мигге-Перроу».
Инфракрасные дефектоскопы |
Инфракрасные дефектоскопы используют инфракрасные (тепловые) лучи для обнаружения непрозрачных для видимого света включений. Так называемое инфракрасное изображение дефекта получают в проходящем, отраженном или собственном излучении исследуемого изделия. Дефектные участки в изделии изменяют тепловой поток. Поток инфракрасного излучения пропускают через изделие и регистрируют его распределение теплочувствительным приемником.
Радиоволновые дефектоскопы |
Радиодефектоскопия основана на проникающих свойствах радиоволн сантиметрового и миллиметрового диапазонов (микрорадиоволн), позволяет выявлять дефекты главным образом на поверхности изделий обычно из неметаллических материалов. Радиодефектоскопия металлических изделий из-за малой проникающей способностью микрорадиоволн ограничено. Этим методом определяют дефекты в стальных листах, прутьях, проволоке в процессе их изготовления, а также измеряют их толщину или диаметр, толщину диэлектрических покрытий и т. Д. От генератора, работающего в непрерывном или импульсном режиме, микрорадиоволн через рупорные антенны проникают в изделие и, пройдя усилитель принятых сигналов, регистрируются приемным устройством.
Электронно-оптические дефектоскопы |
ЭОД предназначены для дистанционного контроля высоковольтного энергетического оборудования, находящегося под напряжением. В основе метода диагностики лежит определение характеристик коронных (КР) и поверхностно-частичных разрядов (ПЧР), а также их зависимостей от величины напряжения и степени загрязнения изоляции.
Капиллярные дефектоскопы |
Капиллярный дефектоскоп представляет собой совокупность приборов капиллярного неразрушающего контроля. Капиллярный контроль основан на искусственном повышении световой и цветовой контрастности дефектного участка относительно неповрежденной. Методы капиллярной дефектоскопии позволяют обнаруживать невооруженным глазом тонкие поверхностные трещины и другие несплошности материала, образующиеся при изготовлении и эксплуатации деталей машин. Полости поверхностных трещин заполняют специальными индикаторными веществами (пенетранта), проникающими в них под действием сил капиллярности. Для так называемого люминесцентного метода пенетранты составляют на основе люминофоров (керосин, нориол[2] и др.) На очищенную от избытка пенетранта поверхность наносят тонкий порошок белого проявителя (окись магния, тальк и т. п.), обладает сорбционными свойствами, за счет чего частицы пенетранта извлекаются из полости трещины на поверхность, изображают контуры трещины и ярко светятся в ультрафиолетовых лучах. При так называемом цветном методе контроля пенетранты составляют на основе керосина с добавлением бензола, скипидара и специальных красителей (например, красной краски).
Толщиномер |
Толщиномер — это измерительный прибор, позволяющий с высокой точностью измерить толщину слоя покрытия металла (такого как краска, лак, грунт, шпаклевка, ржавчина, толщину основной стенки металла, пластмасс, стекла, а также других неметаллических соединений, покрывающих металл). Современные приборы позволяют измерить толщину покрытия без нарушения его целостности.
Применяется в автомобильной, судостроительной промышленности для контроля качества лакокрасочного покрытия транспортных средств, в ремонтных работах, для определения состояния кузова или обшивки по результатам эксплуатации.
В строительстве применяется для определения толщины покрытия металла, имеющего в своем составе противопожарные, антикоррозионные и другие виды компонентов, используемых при создании конструкций зданий.
Толщиномер применяется в работе экспертов-оценщиков, профессиональных полировщиков, контролирующих качество проведения покрасочных работ.
Толщиномеры делятся по принципу их работы, сферы применения, а также способом измерений на:
- механические
- электромагнитные
- ультразвуковые
- магнитные
- вихретоковые
- электромагнитновихретоковые
Течеискатель |
Течеискатель — прибор предназначен для обнаружения, локализации и количественной оценки величины течи. Работа течеискателей может базироваться на различных физических принципах, ориентированных как на прямые, так и на косвенные измерения параметров. Количественную оценку течи производят, как правило, при использовании тестового газа. Для количественной оценки течи используется отношение произведения величины тестируемого объёма на перепад давления в нём до единицы времени.
Гелиевые масспектрометрические течеискатели |
Необходимым условием для использования гелиевых масспектрометрических течеискателей является наличие вакуума в детекторе прибора — в масспектрометр. Согласно течеискатели делят на 2 вида — течеискатели для работы с вакуумированным оборудованием и течеискатели-шнифферы (от англ. Sniffer и нем. Schnüffer — нюхач) с помощью которых фиксируют течи тестового газа с тестируемого объёма в атмосферу. Шнифферы есть дешевле моделями течеискателей и обладают на 4 — 6 порядков более низкой чувствительностью, чем течеискатели на вакууме. Тем не менее большинство течеискателей первого типа комплектуется насадками для защиты входа, которые позволяют им работать в режиме шниффера.
Фреоновые течеискатели |
Фреоновые течеискатели используются для поиска протечек на любом оборудовании, но проигрывают 3 — 4 порядка в чувствительности гелиевым масспектрометричним течеискатель. Принцип действия фреоновых течеискателей основан на адсорбции тестового газа на поверхности датчика. В связи с этим при детектировании крупных протечек фреоновые течеискатели могут сорбировать слишком много фреона и потребуются специальные процедуры для релаксации датчика. С другой стороны работа на атмосферном давлении и простота датчика позволяют создавать ручные портативные течеискатели с чувствительностью до 10 — 7 Вт.
Литература |
- Алешин Н. П., Щербинский В. Г. Радиационная, ультра-звуковая и магнитная дефектоскопии металлоизделий. — М .: Высш.шк., 1991. — 271 с.
- Билокур И. П. Дефектология и неразрушающий контроль .- Киев: Вища шк., 1990. — 207с.
- Адаменко А. А. Современные методы радиационной дефектоскопии. — Киев: Наук. мнение, 1984. — 215 с.
- Герасимов В. Г., Останин Ю. Я., Покровский А. Д. и др. Неразрушающий контроль качества электромагнитными методами. — М .: Энергия, 2008. 215 с.
- Билокур И. П., Коваленко В. А. Дефектоскопия материалов и изделий. — Киев: Техника, 1989. — 192 с.
Примечания |
↑ Магнитно-порошковая дефектоскопия
↑ Нориол
XFumeOET00Rd